top of page

Products
Exceptional Products
The selection of products manufactured by Belden Machine Corporation are not only of the highest quality, but are also available in a variety of options to ensure you find exactly what you’re looking for. With top-of-the-line materials, cutting-edge production technologies and a highly qualified team, we guarantee complete satisfaction.
Assembly Equipment
From simple pick and place to six axis robots with gripper exchange we can accommodate your assembly needs.
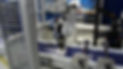

Vision Fixtures
Belden has been using Cognex cameras for over ten years. We take care picking the correct lenes and backlights to view your part.
Tooling
Here at Belden we pride our selfs on the quality of our tooling.

bottom of page